В комплект поставки входит ПО АРМа оператора и
ПО инженерной станции.
ПО инженерной станции устанавливается на отдельный компьютер (например, ноутбук)
и используется при проведении пуско – наладочных работ и режимных испытаний на
отдельном котле. ПО инженерной станции обеспечивает выполнение следующих
основных функций:
-
Проверка функционирования оборудования и
исполнительных механизмов;
-
Индикация показаний датчиков состояния
оборудования и технологических параметров;
-
Выполнение как отдельных, так и нескольких
технологических операций по команде инженера, задание параметров для каждой
операции;
-
Ввод уставок технологических защит;
-
Ввод и вывод защит и блокировок;
-
Ввод заданий для программных регуляторов;
-
Включение / отключение регуляторов;
-
Проведение режимных испытаний.
3.3. Средний уровень
3.3.1. Состав и основные функции
Средний уровень системы включает в себя:
-
до восьми подсистем контроля и
управления котлами, каждая из которых управляет одним котлом и включает в себя
шкаф контроллеров и шкаф приборов;
-
подсистему контроля и управления
вспомогательным оборудованием в составе двух шкафов контроллеров и двух шкафов
регуляторов.
-
подсистему коммерческого учета отпущенной
тепловой энергии и потребленного природного газа в составе шкафа коммерческого
учета, ультразвуковых расходомеров, счетчика расхода газа.
Основным элементом вышеперечисленных подсистем
является микропроцессорный контроллер семейства Микроконт-Р2 (МК-Р2), имеющий
сертификат Госреестра №16682-97.
Оборудование подсистем размещено в шкафах размерами 1650*600*300.
Программное
обеспечение подсистем среднего уровня написано на языке РКС (язык
программирования контроллеров «Мкроконт-Р2», ориентированный на специалистов
автоматчиков и технологов).
Загрузочные модули прикладных программ хранятся в электрически -перезаписываемом
ПЗУ соответствующих процессорных устройств контроллеров (модулей
CPU-320).
Основными функциями контроллеров являются:
-
ввод сигналов от датчиков технологического
процесса и оборудования (дискретные сигналы типа «сухой контакт» и аналоговые
(ток 4-20 mA);
-
передача данных и сообщений на АРМ оператора;
-
прием данных и команд от АРМа оператора;
-
выдача сигналов управления (типа «сухой
контакт») технологическим оборудованием;
-
реализация алгоритмов управления
технологическим оборудованием, технологических блокировок и защит и т.д.
3.3.2.
Подсистемы контроля и управления котлами
Подсистемы
контроля и управления котлами обеспечивают выполнение следующих основных
функций:
-
сбор и первичная
обработка сигналов датчиков параметров технологического процесса;
-
автоматическое
регулирование технологических параметров и поддержание заданной мощности
котла;
-
логическое управление в
соответствии с запрограммированными алгоритмами;
-
реализация защит и
блокировок в соответствии с нормативной документацией на водогрейные котлы
-
передача значений
контролируемых параметров на АРМ оператора;
-
прием и исполнение команд
дистанционного управления от АРМа оператора и местного пульта управления;
-
диагностика состояния
технических средств подсистемы.
Регулирование технологических параметров
выполнено на регуляторах, программно реализованных в контроллерах подсистемы.
Каждый контроллер реализует следующие регуляторы:
-
регулятор давления газа к
горелке;
-
регулятор давления
воздуха к горелке;
-
регулятор разрежения в
топке котла;
-
регулятор соотношения
«газ-воздух».
Первые три регулятора имеют два режима работы:
-
режим поддержания
заданного значения параметра;
-
режим управления
регулирующим клапаном по положению.
В первом случае в качестве обратной связи
используется сигнал с датчика параметра. Данный режим используется при штатном
режиме работы. Второй режим используется при проверке работы регулирующего
клапана и его датчика положения, а также для установки регулирующего клапана в
заданное положение.
Установка режимов работы регуляторов и заданий для их работы производится от
АРМа оператора, либо с местного пульта управления.
Логическое управление реализует алгоритмы управления котлом при пуске и останове
как в автоматическом, так и в ручном (пошаговом) режимах управления.
Для обеспечения безопасной работы котла
реализованы следующие защиты, действующие на останов котла:
-
защита по погасанию
факела;
-
защита на повышение и
понижение давления газа к горелке;
-
защита на понижение
давления воздуха к горелке;
-
защита по отключению
дутьевого вентилятора и дымососа;
-
защита по повышению
давления в топке котла;
-
защита по повышению и
понижению давления воды за котлом;
-
защита по понижению
расхода воды через котел;
-
защита по повышению
температуры воды за котлом;
-
защита по невоспламенению
при растопке.
Ввод защит производится автоматически по
определенным условиям. Все защиты, кроме последней, могут быть выведены по
командам с АРМа оператора. При отмене команд вывода защиты автоматически
вводятся.
К командам дистанционного управления относятся команды типа «включить /
выключить клапан», «открыть / закрыть задвижку». По командам от АРМа оператора
контроллер отрабатывает соответствующий алгоритм и выдает сообщение на АРМ
оператора о результате его выполнения («выполнено» или «авария»).
В состав каждой подсистемы входят
шкаф контроллера и шкаф приборов. В шкафу контроллера установлено следующее
оборудование:
-
микропроцессорный контроллер в составе:
-
модуль центрального процессора
CPU-320DS;
-
модуль ввода аналоговых сигналов
Ai NOR/RTD-170;
-
модуль ввода дискретных сигналов
Bi32
DC24;
-
модуль вывода дискретных сигналов
Bo32DC24.
-
источники питания ~220В/=24В и ~220В/=36В,
промежуточные реле, автоматические выключатели, клеммники, источник
бесперебойного питания;
На лицевой
двери шкафа установлен пульт оператора.
В шкафу приборов установлены
бесконтактные реверсивные пускатели ПБР-2М и ПБР-3А, используемые для
управления клапанами и электроисполнительными механизмами типа МЭО; блоки
питания БП-10 и БП-24 для питания датчиков положения с токовым выходом, которыми
укомплектованы МЭО; электронный блок ультразвукового расходомера
US-800,
обеспечивающий расчет расхода воды на входе котла; автоматические выключатели и
клеммники для внешних подключений.
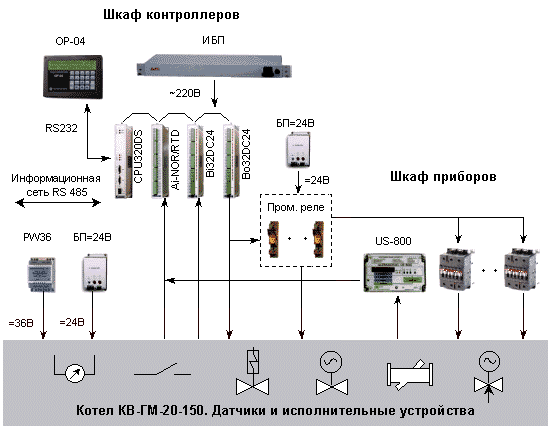
Рис.5 Подсистема
контроля и управления котлом. Структурная схема.
3.3.3. Подсистема контроля и управления
вспомогательным оборудованием
Подсистема контроля и управления
вспомогательным оборудованием обеспечивает выполнение следующих основных
функций:
-
сбор и первичная
обработка сигналов датчиков параметров технологического процесса;
-
автоматическое
регулирование технологических параметров;
-
логическое управление в
соответствии с запрограммированными алгоритмами;
-
реализация защит и
блокировок;
-
передача значений
контролируемых параметров на АРМ оператора;
-
прием и исполнение команд
дистанционного управления от АРМа оператора и местного пульта управления;
-
диагностика состояния
технических средств подсистемы.
В подсистеме программно реализованы 14
следующих регуляторов:
-
Регулятор температуры
воды в подающем магистральном трубопроводе в зависимости от температуры
наружного воздуха.
-
Регулятор давления
подпиточной воды.
-
Регулятор температуры
обратной сетевой воды перед котлами.
-
Регулятор давления воды
на всасе сетевых насосов.
-
Регулятор разрежения в
деаэраторе.
-
Регулятор температуры
очищенной воды за подогревателем.
-
Регулятор температуры
очищенной воды перед деаэратором.
-
Регулятор температуры в
деаэраторе.
-
Регулятор температуры
воды в системе горячего водоснабжения.
-
Регулятор температуры
газа в котельную.
-
Четыре регулятора воздуха приточной
вентиляции.
Программное обеспечение подсистемы
обеспечивает функционально – логическое управление следующим оборудованием
котельной:
-
Сетевые насосы (4 шт.);
-
Задвижки на напоре
сетевых насосов (4 шт.);
-
Насосы рециркуляции (4
шт.);
-
Насосы рабочей воды (2
шт.);
-
Насосы деаэрируемой воды
(2 шт.);
-
Насосы подпиточной воды
(2 шт.);
-
Насос откачки воды и
герметика;
-
Насос герметизирующей
жидкости;
-
Магистральные задвижки (2
шт.);
-
Клапан подачи воды в бак
чистой воды;
Кроме этого обеспечивается контроль
загазованности в помещении ГРУ и котельной.
К командам дистанционного управления относятся
команды типа «включить / выключить насос», «открыть / закрыть задвижку». По
командам от АРМа оператора контроллер отрабатывает соответствующий алгоритм и
выдает сообщение на АРМ оператора о результате его выполнения («выполнено» или
«авария»).
Подсистема включает в себя:
-
два шкафа контроллеров;
-
два шкафа приборов.
Микропроцессорные контроллеры объединены
дополнительной информационной сетью на базе промышленного стандарта
RS485.
Необходимость этого вызвано тем, что алгоритмы управления вспомогательным
оборудованием (выдача сигналов управления) реализованы в контроллере 1, а
контроллер 2 реализует только функции ввода дискретных и аналоговых сигналов.
При этом оба контроллера имеют связь с АРМом оператора по основной
информационной сети системы.
В шкафах приборов установлены бесконтактные реверсивные пускатели ПБР-2М и
ПБР-3А, используемые для управления клапанами и электроисполнительными
механизмами типа МЭО; блоки питания БП-10 и БП-24 для питания датчиков положения
с токовым выходом, которыми укомплектованы МЭО; автоматические выключатели и
клеммники для внешних подключений.
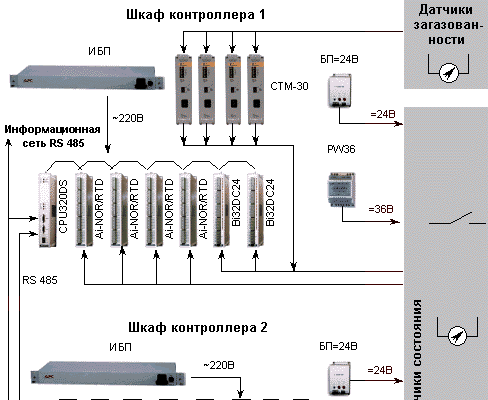
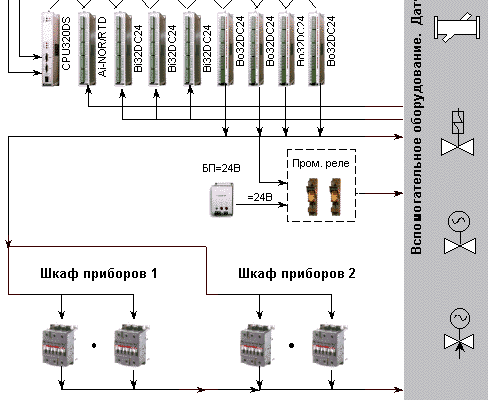
Рис.6
Подсистема контроля и управления вспомогательным оборудованием. Структурная
схема.
3.3.4. Подсистема коммерческого учета
Подсистема коммерческого учета предназначена
для организации технологического контроля и коммерческого учета отпущенной
тепловой энергии, потребления холодной воды и природного газа.
Основным элементом подсистемы (см.рис.4) является теплосчетчик
HC-200WT
(№17972-98 в Госреестре средств измерений РФ), обеспечивающий расчет количества
отпущенной тепловой энергии, количества теплоносителя и потребленной холодной
воды. Измерение расхода теплоносителя и холодной воды обеспечивают
ультразвуковые расходомеры
US-800. Информация о величине расхода в
виде токового сигнала передается в теплосчетчик. Измерение параметров горячей и
холодной воды обеспечивается датчиками давления типа МИДА-ДИ и датчиками
температуры типа КТПТР, подключенных непосредственно к теплосчетчику.
Измерительные участки расходомеров, датчики давления и температуры установлены
на соответствующих участках трубопроводов котельной (прямая и обратная сетевая
вода, подпиточная и исходная вода). Теплосчетчик
HC-200WT,
электронные блоки расходомеров
US-800
установлены в шкафу приборов коммерческого учета. В этом же шкафу расположены
блоки питания ~220В/=36В (PW
36-0,05SP),
служащие для питания датчиков давления МИДА-ДИ.
Для измерения параметров и расхода природного газа используется расходомер –
счетчик газа ВРСГ-1, электронный блок которого установлен в шкафу коммерческого
учета.
Передача информации (используемой как для
технологического контроля, так и для коммерческих расчетов) с теплосчетчикаHC-200WT
на АРМ оператора осуществляется по информационной сети системы. Для организации
передачи информации с расходомера – счетчика газа ВРСГ-1 используется модуль
CPU-320DS,
выполняющий роль конвертора протоколов (модуль – шлюз).
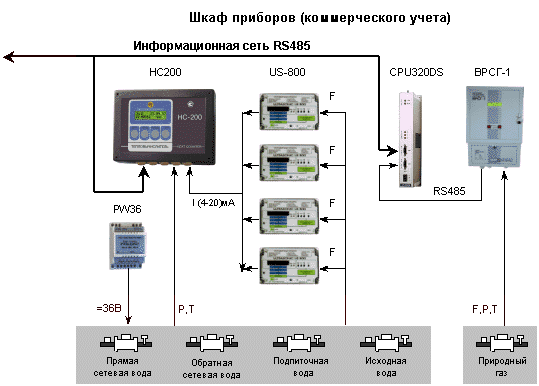
Рис.7
Подсистема коммерческого учета. Структурная схема.
3.4. Полевая информационная
шина
Полевая информационная шина обеспечивает обмен
данными между подсистемами среднего уровня и АРМом оператора.
Основные характеристики информационной сети:
|
«главный-подчиненные» (master-slave); |
Организация шины в виде петли с отдельным
каналом управления на каждом ее конце обеспечивает работоспособность всей
сети в случае обрыва шины связи.